
RECOIN CABLE
Short Description:
Recoin's 8-shaped fiber optic cable has a structure that best meets the technical requirements stipulated in national and international standards.
PRODUCT DESCRIPTION
TECHNICAL STANDARDS FOR OPTICAL CABLE
General Introduction
- Recoin's metal and non-metal hanging optical cables use single-mode optical fibers, placed in moisture-proof oil-filled loose tubes, with moisture barriers, a protective sheath for non-metallic cables, and two protective sheaths for metallic cables, galvanized steel braided hanging wires. Fiber capacity from 2 to 144 optical fibers.
- Recoin cables fully comply with international standards IEC, EIA, ASTM, national standards TCVN, industry standards TCN, or customer standards...
Product Sign
Non-steel band hanging cable: TPKL 2C - 144C
Steel band hanging cable: TKL 2C - 144C
Simulation of the structure of non-steel band hanging optical cable (TPKL)
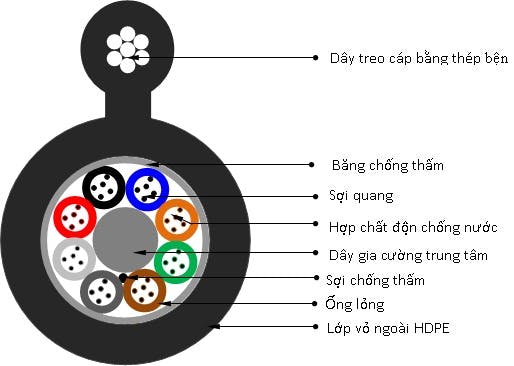

Technical characteristics of single mode fiber G 652D

Detailed components of the cable
The optical fiber used is single mode G.652D, step-index.
The outer layer of the optical fiber is color-coded according to TIA/EIA-598-A standard.
The primary coating and the outer ink of the optical fiber use ultraviolet-resistant material (acrylate), minimizing the impact of the external environment and lasting over time.
When splicing, the primary coating can be easily stripped using specialized equipment without chemicals, without affecting the fiber.
Components of the optical fiber such as core, sheath, ink... are non-conductive.
The standard parameters of the optical fiber are specified as above table.
All optical fibers used in one cable are from a single optical fiber manufacturer.
The color coding rule of the optical fibers in the same loose tube is specified as the table below:
Fiber Type | Single mode, G.652D |
Mode Field Diameter | 9.2 µm/ ±0.5µm
10.4 µm/ ±0.8µm + At 1310 nm wavelength/ tolerance + At 1550 nm wavelength/ tolerance |
Cladding Diameter/ Tolerance | 125.0µm/ ±1µm |
Core Concentricity Error | ≤ 0.5µm |
Cladding Non-Circularity | ≤ 1% |
Outer Coating Diameter | 245 ± 5µm |
Cutoff Wavelength | ≤ 1260 nm |
Attenuation Coefficient | ≤ 0.36 dB/km
≤ 0.35 dB/km
≤ 0.22 dB/km
≤ 0.21 dB/km - At 1310nm wavelength + Maximum + Average - At 1550nm wavelength + Maximum + Average |
Dispersion Coefficient | ≤ 3.5 ps/nm´km
≤ 18 ps/nm´km - At 1310nm wavelength - At 1550nm wavelength |
Zero Dispersion Wavelength | 1300 nm ≤ l0 ≤1324 nm |
Zero Dispersion Slope | ≤ 0.092 ps/nm2´km |
PMD Coefficient – Cabled Fiber | ≤ 0.2 ps/ |
Made from non-metallic FRP (Fiber Reinforce Plastic) material, circular, continuous, non-conductive, without any defects. May be coated with PE if necessary to create uniformity for the cable.
This component helps the cable and optical fibers not to be overly stressed and ensures cable flexibility during manufacturing, transportation, installation, and usage.
The loose tube is made from Polybutylene Terephthalate (PBT) material, non-conductive. The loose tubes in a cable are color-coded according to EIA/TIA-598 standard and are specified as the table below.
This loose tube contains optical fibers inside and is filled with a specialized moisture-proof compound (filling compound). The optical fibers are free and move easily.
The loose tube is continuously fabricated, with a smooth surface, no bubbles, no wrinkles, no impurities.
The filler rods are made from high-density Polyethylene (HDPE), non-conductive, color-coded, ensuring the overall roundness for the cable structure.
These filler rods are solid, without bubbles, no impurities, smooth surface.
The jelly compound used to fill the loose tubes and the cable core is specialized for optical cables, maintaining its properties at temperatures from -30°C to +70°C. It is anti-fungus, anti-rodent, water-blocking, non-conductive.
This component includes moisture barriers, ensuring the cable is water-blocking. All materials are non-conductive.
The optical cable core is stranded in a circular shape, providing the highest strength and flexibility.
For metallic cables, galvanized steel wire braid is used. For non-metallic cables, aramid yarn is used for additional reinforcement.
A protective layer of corrugated steel tape can be used to enhance cable protection, ensuring the cable is not overly stressed and can withstand external mechanical impacts.
The outer sheath is made from black high-density Polyethylene (HDPE), ensuring the cable's mechanical strength and protecting the internal components from external environmental impacts.
For metallic cables, galvanized steel wire is used for hanging. For non-metallic cables, aramid yarn is used. The hanging wire ensures the cable is securely fastened during installation.